There are many kinds of laboratory ball mills, like lab cylinder cone crushers, lab cone ball mills, lab rod mills, etc. The lab stirring ball mill is one of the machines for the ultra-fine grinding process. Stirring ball mills are composed of stationary grinding cylinders filled with small-diameter grinding media, mixing devices, and other devices (such as cooling devices, timing, speed control, etc.). They have high grinding efficiency, and small crushing particle size, meet process parameter requirements, and simulate various indicators in production. At the same time, due to the advantages of small batch size and low power consumption, it is widely used by schools, research units, and companies to research crushing processes, new materials, and coatings.
Application of stirring ball mill
This machine is for the ultrafine grinding process of coatings, magnetic materials, paints, inks, dyes, ferrites, and food.
- Wet fine grinding: re-grinding of gold, silver, molybdenum, uranium, copper, and lead-zinc ores. Fine or ultrafine grinding of calcium carbonate, kaolin, mica, talc, barite, iron, graphite, coal, ferrite, zircon sand, manganese, manganese dioxide, and coal.
- Dry fine grinding: non-metallic minerals and chemical raw materials such as calcium carbonate, mica, lightly burned magnesium powder, barite, slag, etc.
Structure and working principle
Main structure of stirring ball mill
It mainly consists of an electric motor, pulley, reducer, elastic coupling, stirring shaft, stirring cylinder, etc.
Working principle
This machine is driven by an electric motor (via a pulley)and a deceleration device to rotate a stirring shaft, making the material and grinding medium grind in an irregular motion state. This process produces a strong grinding effect, achieving the goal of ultra-fine process of materials.
3. Conditions of Use
The motor power supply requires a three-phase AC power of 380 volts and 50 hertz.
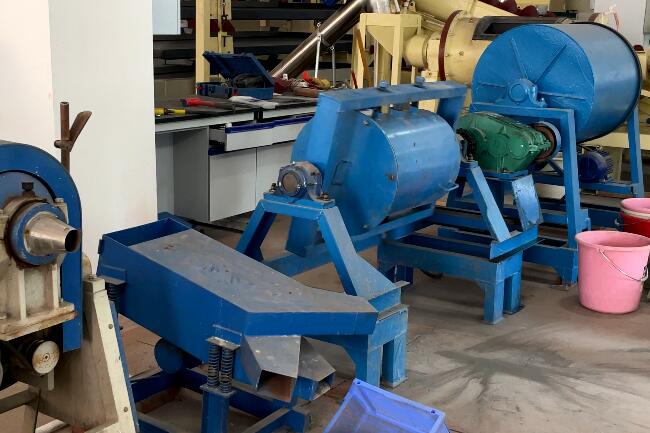
Operation and Maintenance
- Add additives (such as embrittlement agents) or adjust the size ratio of the grinding medium according to the user’s needs.
- When loading and discharging materials, shut down the machine. Before starting the machine, check the tightness of the cylinder cover plate.
- After the sample grinding process finishes and the machine stops, remove the clamping bolt and turn out the cylinder material from the discharge port.
- When replacing the sample, it is necessary to thoroughly clean the grinding medium inside the inner cylinder and the working surface with water to reduce pollution. When the required processing materials are different types of minerals (metallic or non-metallic), one must choose the appropriate grinding medium, grinding cylinder, and stirring shaft based on the material sample.
- Regularly add lubricating oil or grease to the gearbox and bearing position.
Operation Test
After completing the stirring ball mill installation, confirm there is no jamming phenomenon and start testing. The machine should undergo a 2-4 hour no-load and a 5-6 hour load test.
- Empty load test
The no-load test machine must meet the following requirements without feeding.
- Test running of the electrical interlocking system, according to the starting program, confirms the starting and stopping functions meet the design requirements of the electrical interlocking system.
- All fasteners are firm and reliable, without any looseness.
- The flywheel rotates smoothly.
- The temperature rise of the bearing shall not exceed 300C.
- Check if the bearing lubrication is regular, and confirm no oil leakage.
- Load testing
After passing the no-load test, then start the load test. In addition to meeting the requirements for no-load testing, it should meet the following requirements.
- There should be no vibration or abnormal noise. If it occurs, stop the machine immediately, find the cause, and eliminate the fault.
- The feeding position is correct, the discharge is normal, and the product particle size and output meet the requirements.
Advantages of Stirring Ball Mill
- High energy utilization rate, achieve good power density, thus saving energy.
- The particle size is easy to adjust, and we can check the fineness by adjusting the retention time of the material in the cylinder.
- Low vibration and low noise.
- It has the advantages of beautiful design, excellent performance, simple maintenance, and ease of operation.
- The mixing rod can be lifted or lowered automatically, and the grinding barrel can flip freely.
- It meets various process requirements and carries out continuous or intermittent production according to needs.
- Due to the inclusion of a jacket in the ball mill, the grinding temperature is adjustable and well under control.
- Provide devices with other functions such as timing, speed regulation, and temperature regulation.
- You can choose different materials for the cylinder. (stainless steel, corundum ceramics, polyurethane, zirconia, etc.)
JXSC lab mineral processing equipment manufacturer has more than 38 years of experience in mining processing. We provide various lab mining equipment including gravity-separating equipment for processing minerals such as gold, tin, tungsten, lead, zinc, tantalum, niobium, iron, manganese, silver, titanium-iron, etc. Lab machines include laboratory jaw crusher, hammer crusher, roller crusher, grinding equipment, lab gravity separator, screening, washing equipment, etc. Welcome to consult!